How to Do Maintenance of Marine Heat Exchanger On Ships
- Joe Malvisto
- Jan 5, 2021
- 3 min read
Maintenance of marine heat exchanger systems is similar to the maintenance of other heat exchanger systems. The primary difference is that these systems are designed to function in extreme temperatures and there are many specific procedures that must be followed in order to make sure that the system works properly. Marine heat exchanger systems are no different from other non-marine heat exchanger systems except for the fact that they are usually located aboard ships. Heat exchanger systems can be used for various purposes.

When most people think of a marine heat exchanger, they either picture a large pipe system with a number of tubes where water is heated and then returned to the bottom of the pipe system. This is not the only way to heat a fluid but it is one of the most efficient. In addition, there is the option of using an evaporator to heat the tubing. There are some marine heat exchanger systems that are cooled by the use of liquid cooling as opposed to air cooling.
Most people think that the maintenance of these systems is just a matter of replacing worn-out parts. This is not necessarily true because some parts may have been installed incorrectly. The problem with overheating and corrosion are that the original design of the heat exchanger resulted in a "closed" design where the refrigerant gas is allowed to enter and then leaves the system through a pump or by using a pressure vessel. As time progresses this open design will allow a constant supply of refrigerant gas to the system and this will cause overheating and possible damage to the components.
When it comes to equipment such as these, the term lubrication is important. The term "lube" means a specific liquid and it has an added component - an oily component. When it comes to marine equipment, this means the lubricant that is used in these tube heat exchanger tubes. In order for this lubricant to function properly, it must be heated to a specific temperature. This is done by adding distilled water to the lubricant so that it becomes a gas and is moved into the heating system where it heats up and passes through the cooling tubes.
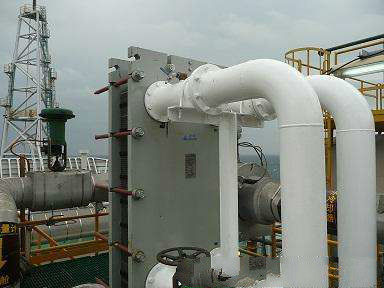
The most important part of the maintenance of marine heat exchanger maintenance involves testing the equipment. During testing, certain parameters must be monitored and a chart and data sheet must be created to track these parameters during the testing process. The testing chart and datasheet will help the maintenance manager identify problems that he or she might not otherwise be aware of. These charts can also be useful when it comes to explaining to the operator what is being tested and why.
If your business uses these marine heat exchanger systems, it is important to be knowledgeable about how to maintain them. Keeping an eye on the performance of these pieces of equipment is only as effective as its care and maintenance. If you want to minimize downtime and keep the unit working efficiently, be sure to follow the manufacturer's maintenance instructions carefully. Take care of the units by cleaning them regularly using mild detergents. Remember to add lubricant when necessary and perform regular tests to make sure all components are operating according to the manufacturer's specifications.
Read More: The Benefits of a Plate Heat Exchange Unit
View more here: Promec Engineering Pty Ltd
Comments